Le PLUS DE PUS
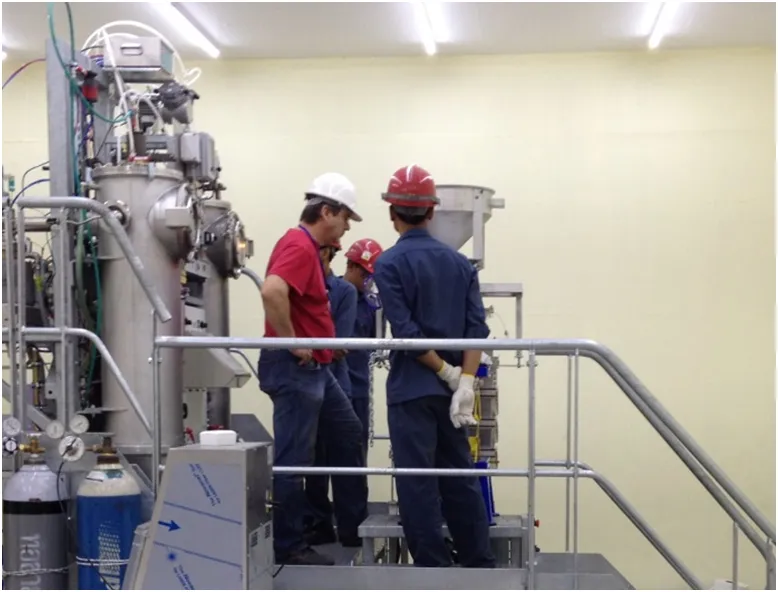
Listening to market changes, PUS understood that specific alloys were needed for each type of soldering. The PUS atomizer is particularly suitable for small and medium volume manufacturing for these specific alloys.
PUS wants to be an independent and pragmatic advice on the true performance of these alloys, far from the commercial fashion or patents.
OUR VIEW: On copper pads, the classical IMC that is formed after soldering using a SAC alloy is Sn5Cu6. The shape of this IMC is usually a needle shape. Furthermore, IMC is always a brittle material. This is actually harmful for drop test behavior where breakage will occur near this IMC layer.
OUR VIEW: Lead Rich alloys are still widely used, especially for die attach. A simple lead free alternative doesn’t exist into nature where BiAg based alloys will lead to poor wetting, SnSb with Sb lower than 10% may have a too low melting point and Zn based alloys can lead either to poor wetting or large IMC.